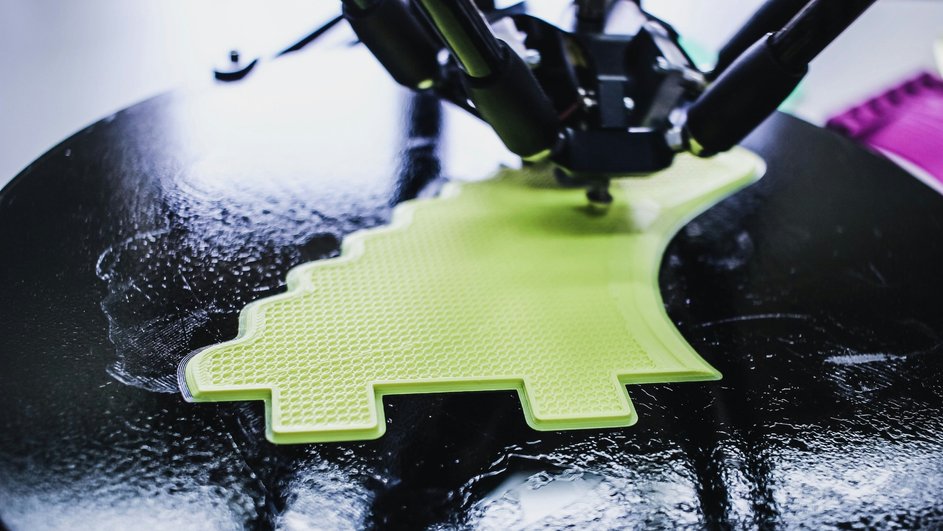
Технология 3D-печати металлов основывается на послойном нанесении металлических материалов с использованием тепла для их соединения. Этот метод позволяет создавать уникальные, высокоадаптивные формы с минимальными отходами, что делает его привлекательным для промышленного применения. Одним из ключевых преимуществ 3D-печати является возможность создавать многоматериальные структуры, где разные материалы объединяются для достижения оптимальных характеристик изделия. Например, в автомобильной промышленности использование алюминия в сочетании со сталью может существенно снизить вес деталей без ущерба для их прочности. Однако реализация подобных технологий сталкивается с рядом сложностей.
«Многоматериальные структуры — это горячая тема в области аддитивного производства благодаря гибкости процесса», — объясняет доцент Кента Яманака из Университета Тохоку. «Тем не менее, одна из главных проблем при их внедрении — образование хрупких интерметаллических соединений на границе различных металлов, например, стали и алюминия. В результате материал, хотя и становится легче, теряет в прочности».
Целью исследования стало создание стально-алюминиевого сплава, который сохранял бы прочность при снижении веса. Для этого команда использовала технологию лазерного плавления порошков (Laser Powder Bed Fusion, L-PBF) — одну из основных технологий 3D-печати металлов. Этот метод предусматривает выборочное плавление металлических порошков при помощи лазера. Ученые обнаружили, что увеличение скорости сканирования лазера значительно подавляет образование хрупких интерметаллических соединений. Они предположили, что высокая скорость сканирования способствует процессу неравновесной кристаллизации, минимизируя разделение элементов, что обычно создает слабые точки в материале. Таким образом, удалось добиться прочного соединения металлов.
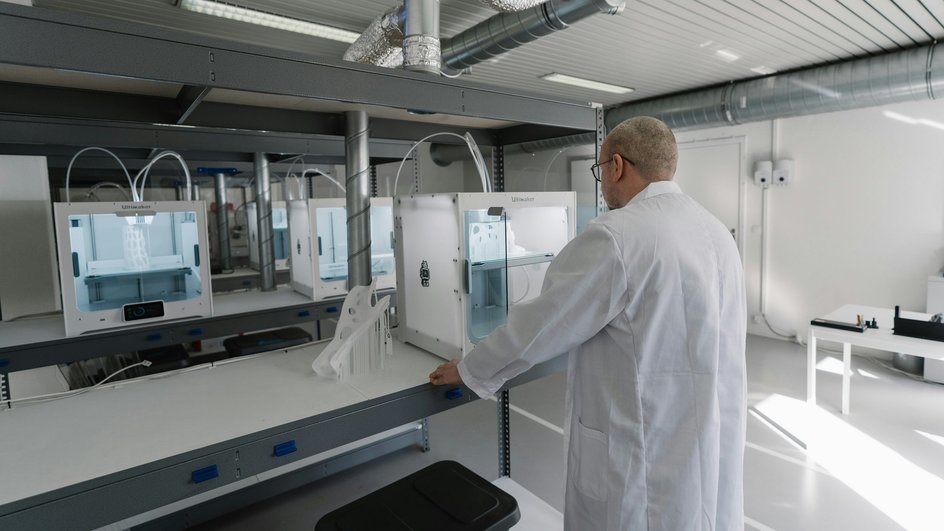
«Просто соединить два металла недостаточно — без тщательной подготовки они не будут держаться вместе», — поясняет специально приглашенный ассистент-профессор Сынгкюн Йим. «Мы сначала должны были глубоко понять механизм сплавообразования в процессе печати».
Благодаря этим открытиям исследователи разработали первый в мире полномасштабный прототип многоматериальной автомобильной детали — опоры подвески с оптимизированной геометрией. В дальнейшем они планируют применить полученные знания к другим комбинациям металлов, чтобы устранить проблемы соединения и расширить область применения технологии. Этот прорыв открывает новые горизонты для создания высокоэффективных компонентов в автомобильной промышленности и других отраслях, где требуется сочетание легкости и прочности.
Тем временем в Томске появился 3D-принтер для печати зданий.